A Fe-Ni-Cr alloy with excellent high temperature oxidation resistance
- Good material for high temperature oxidation resistance
- Maintains high strength at elevated temperatures
- A286 Chemistry, specs and heat treatments
- Lap joint flange features and benefits
A-286 lap joint flanges are known for their high strength, creep resistance and oxidation resistance at elevated temperatures. This iron-nickel-chromium alloy (once age-hardened) provides A-286 lap joint flanges with high levels of strength from room temperature up to about 1300°F (700°C).
A-286 lap joint flanges are mildly corrosion resistant. While they should not be used for strong acid environments, they provide excellent oxidation resistance up to 1300°F (700°C) in conditions that would typically be found in high temperature exhaust streams.
Because of these properties, A-286 lap joint flanges are often found in high temperature engine, manifold, exhaust and turbine applications as well as off-shore oil & gas applications.
Resources: A-286 Torque Specs, Flange Dimensions, Flange Bolting Chart
Flange Types Available: Blind Flanges, Lap Joint Flanges, Slip On Flanges, Socket Weld Flanges, Threaded Flanges, Weld Neck Flanges
A-286 Chemistry, Specifications & Heat Treatments
A-286 Heat Treatments: There are several heat treatment combinations for A-286 all with slight variations in performance. They can be specified via an AMS number or a 660 Class: A, B, C or D, with most common specified as class A or D. The A-286 grades A, B and C all have the same min tensile strength and min yield strength of 130ksi and 85ksi respectively. However grade D is significantly better yield with a min tensile of 130ksi and a min yield of 105ksi.
By AMS numbers, the most common for A-286 is AMS 5737 (same as Grade A) and then AMS 5732 (same as Grade B).
A-286 Specifications: AMS 5525, AMS 5732, AMS 5737, AMS 5804, EN 1.4980, GE B50T1181, GE B50T12, GE B50T81, UNS S66286, Werkstoff 1.4980
Mechanical Properties
A286 Lap Joint Flange Features & Benefits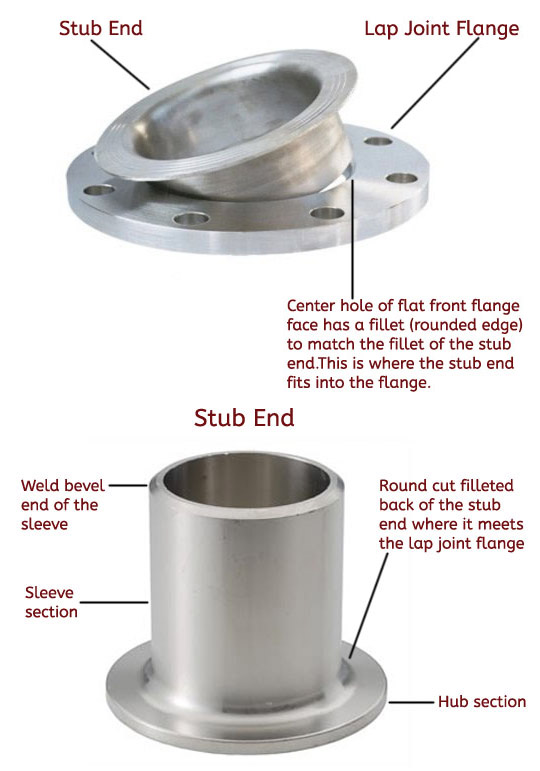
Lap joint flanges are unique in that they are made of two pieces, the flange itself and the stub end.
Flange
- The backside, has a slight shoulder that is square cut at the center or pipe hole
- The front side has a flat face with a filleted (rounded) center hole to match the filleted back face of the stub end. Here the stub end will wrap tightly around the center hole of the flange.
Stub End
- Shaped like a short piece of pipe with a weld bevel on one. This portion of the stub end is also called the sleeve.
- Narrow shoulder on the flange facing end called is the hub. The back face of the hub has a rounded transition (or inside fillet) that joins the hub to the sleeve
Benefits
- Economy
Because a lap joint flange has a two piece configuration, it offers a way to cut cost when piping systems requires - For high cost alloys the only "wetted" part is the stub end. In this situation, it is only required for the stub-end to be made of the higher cost corrosion-resistant material, where the flange itself can be the produced from lower cost steel.
- Ease of Work
By using lap joint flanges, work can be simplified in situations that require frequent and rapid disassemble and assembly during the operation of a plant. The ability to spin that backing flange compensates for misalignment of the bolt holes during assembly.