An extremely strong precipitation hardened stainless steel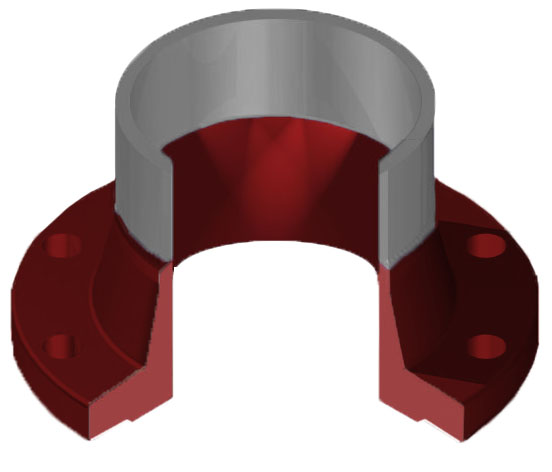
- Well suited for high strength applications
- Up to 4x stronger than 316 stainless steel
- Maintains its mechanical strength up to 600°F
- 17-4PH Chemistry & Specifications
- ASTM F593 Gr 630
- ASTM A564 Gr 630
- Weld neck flange features and benefits
17-4 PH weld neck flanges are made from a precipitation hardened stainless steel most known for its exceptional strength and its ability to maintain its mechanical properties to 600°F. Compared to 316 stainless steel, 17-4 PH weld neck flanges yield strength is up over 4 times greater. When compared to Duplex 2205 weld neck flanges, the yield strength of 17-4 PH can be up to 2-½ times greater.
17-4 weld neck flanges are available in 8 different aged (precipitation hardened) conditions offering a variety of mechanical properties (see below).
Resources: 17-4PH Torque Specs, Flange Dimensions, Flange Bolting Chart
Flange Types Available: Blind Flanges, Lap Joint Flanges, Slip On Flanges, Socket Weld Flanges, Threaded Flanges, Weld Neck Flanges
17-4PH Chemistry & Specifications
17-4PH Specifications: UNS S17400, AISI 630, ASTM A564-630, Werkstoff 1.4542, AMS 5604 Sheet, Strip and Plate, ASTM A 693 Plate
ASTM F593, Grade 630
This specification covers seven groups of stainless steel alloys, with ASTM F593, Grade 630 applying 17-4PH. ASTM F593 Grade 630 covers the requirements for 17-4PH stainless steel bolts, hex cap screws, and studs sized 0.25 to 1.50 inches, inclusive, in nominal diameter. It is intended for common use and for service applications requiring general corrosion resistance.
Common 17-4 Flange Conditions: Aged Conditions vs Tensile Strength
ASTM A564 GR 630
This specification covers bars and shapes (such as fasteners) of age hardened stainless steels such as 17-4PH. It includes hot-finished or cold-finished fasteners that are produced by hot rolling, extruding, or forging. Grade 630 shall be furnished in the solution-annealed or or age-hardened condition.
17-4 PH Weld Neck Flange Features & Benefits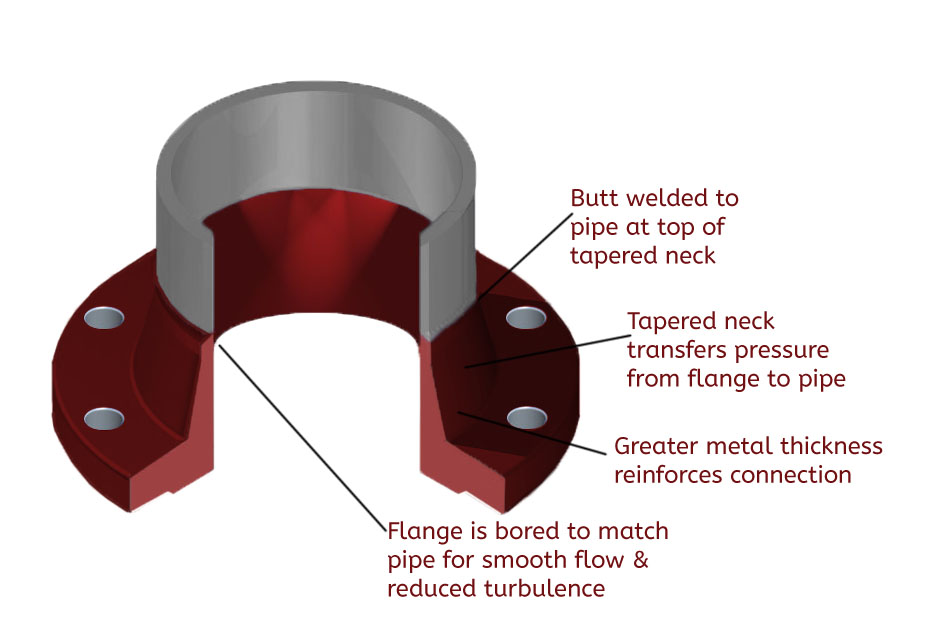
17-4 PH weld neck flanges are best for hazardous, high pressure applications. Weld neck flanges are easily identified by their long tapered neck. The inside of the flange is bored to match the inside diameter of the pipe in order to ensure there is no restriction in flow and also to prevent turbulence at the joint. The tapered neck provides thicker metal at the flange joint, while the neck narrows down gradually to meet the pipe where it is butt welded to the pipe. This design helps to transfer stress from the flange to the pipe, as well as diminish stress concentration at the base of the flange connection.
17-4 PH weld neck flanges are ideal for critical applications involving high pressure, sub-zero and elevated temperatures, as well as in conditions where fluctuations cause pipe expansion/contraction.
Key Feature: Ideal for high presure applications.
Weld Neck Flange Advantages
- Ability to withstand high pressure – since pipe is welded to the neck of the flange, stress is transferred to the pipe.
- The beveled end that, when connected to a pipe, creates a trough for a strong weld.
- Most versatile flange in the ASME stable of flanges.
Weld Neck Flange Disadvantages
- More advanced welding skill is needed for installation. The inside weld must be smooth to reduce friction and the outside weld must meet code criteria.
Uses
- Severe conditions that include high-pressure, high-cyclic and hazardous fluid applications.
- Fitting-to-fitting fabrication where the flange is welded directly to a fitting, such as an elbow, without the need for a short piece of pipe, as would be required with a slip-on flange.