Good high temperature oxidation resistance to 2000°F
High temperature stability for moderate strength applications- Good oxidation and carburization resistant to 2000°F
- Resistance to moderate sulfidation and nitriding
- Economic alternative to high temperature nickel alloys
- 310SS chemistry & specifications
- Features & benefits of 310SS threaded flanges
- Datasheet for 310 stainless steel
Designed for high temperature applications, 310 stainless steel threaded flanges provide high temperature oxidation resistance to 2000°F under mild cyclic conditions. An economic alternative to nickel alloys like alloy 330 or Inconel, 310 flanges provide slightly less strength and temperature resistance – but at a significantly lower price point. Alloy 310 can be used in moderately caburizing, moderately oxidizing, nitriding, cementing and thermal cycling applications when not used at the maximum service temperature. 310SS threaded flanges also have good resistance to sulfidation and other forms of hot corrosion. Although primarily known for its high temperature properties, 310 stainless steel also provides excellent performance at cryogenic temperatures, with toughness down to -450˚F. Though 310 threaded flanges are ideal for high temperature use, they should not be exposed to the severe thermal shock of repeated liquid quenching or where aqueous corrosive contaminants are present.
Benefits
- High temperature resistance.
- Excellent resistance to oxidation under mildly cyclic conditions.
- Good resistance to sulfidation and atmospheres where sulfur dioxide gas is encountered at elevated temperatures.
- Good resistance to thermal fatigue.
- Excellent toughness to cryogenic temperatures of -450°F.
- Low magnetic permeability.
- Good ductility and weldability.
Applications
- Thermal processing and high temperature furnaces rely on 310 flanges for their high temperature and oxidation resistance in minor cyclic conditions.
- 310SS threaded flanges are commonly used in the petrochemical industry for their ability to provide resistance to moderately carburizing atmospheres.
- The high temperature properties of 310 threaded flanges make them ideal for ore processing, steel plants, power generation, and sintering.
- Cryogenic structures often use 310 stainless steel flanges for their strength at -450°F and low magnetic permeability.
310 Stainless Steel Properties | |
Tensile Strength (ksi) | 70 |
Yield Strength (ksi) | 30 |
Rockwell B Hardness | 95 |
Density (lb/in3) | 0.285 |
Electrical Resistivity (Microhm-in at 68°C) | 30.7 |
Modulus of Elasticity (x 106 psi) | 28.5 |
Thermal Conductivity at 212°F (BTU/hr/ft2/ft/°F) | 8.0 |
Resources: Flange Dimensions, Flange Bolting Chart
Alloy 310 Bolt Types: Blind Flanges, Lap Joint Flanges, Slip On Flanges, Socket Weld Flanges, Threaded Flanges, Weld Neck Flanges
310 Stainless Steel Chemistry & Specifications
310SS Specifications: AMS 5521, AMS 5651, ASME SA 240, ASME SA 312, ASME SA 479, ASTM A 240, ASTM A 276, ASTM A 276 Condition A, ASTM A 276 Condition S, ASTM A 312, ASTM A 479, EN 10095, UNS S31008, UNS S31009, Werkstoff 1.4845
310SS Threaded Flange Features & Benefits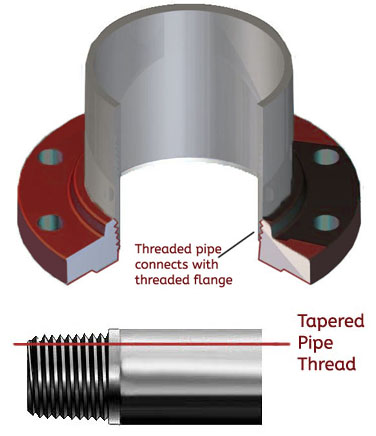
310 threaded flanges have a tapered female thread to join the male threads of a pipe in order to create a tight seal. This type of flange is most ideal when post weld heat treatment is not possible in hazardous, flammable or explosive applications where welding is too dangerous. 310SS threaded flanges are also convenient in pilot processes whose configuration is often changed.
Threaded Flange Advangtages
- The main benefit is that that threaded seal eliminates the need for welding.
- As they do not require welding they save time and money to install.
- Allow for connections to be made in dangerous, explosive applications where welding is not possible.
- Useful connection in materials that are difficult to create a successful and strong weld.
- Ideal for connecting small diameter pipes.
- Systems could be easily reconfigured.
Threaded Flange Disadvantages
- They are not suitable where high temperatures, frequent cyclic conditions or bending stresses are likely in applications.
Best Thread for Your Specific NeedsBolt threading has a huge impact on the performance of a fastener. There are many options when it comes to threading. But let start with the basics and explore the different threading options Extreme Bolt offers. Fine and Coarse Threads Coarse threads are denoted by the standard UNC. A bolt with coarse threads has less threads per inch than a fine thread – so the threads are further apart. Coarse threads work for most applications and are the most common. In contrast, fine threads offer more threads per inch. They are denoted by the standard UNF. Bolts with fine threads provide more grip as the threads are closer together and there are more threads to hold the bolt in place. Fine threads are typically required for applications that require greater security and tighter tolerances. Understanding Thread Tolerance and Classes Threads are categorized into 3 classes that denote the thread tolerance for the pitch: 1, 2 and 3. Class 1 has the loosest tolerance whereas 3 has the most precise. Class 2 is often most common for standard applications. In addition to the classes, there are letters assigned to denote internal verses external threads. The letter A is assigned to external threads so threading on bolts, screws, rod and studs: classes are 1A, 2A and 3A. The letter B is assigned to internal threading for nuts, which include 1B, 2B and 3B.
Rolled Threads Compared to Machined Threads Machined threads refer to the internal root and flank of the thread being cut away to create the thread form. In contrast, rolled threads means the threads are formed by pressing the parts between two round dies or flat plates that already have the thread pitch machined onto their face. When the parts move, or roll, through the dies, the threads are formed by the applied pressure without cutting or removing any material. When threads are rolled, it creates a rounded root radius. Also, the cold working process of the thread rolling operation increases the strength of the material within the threads. For non-heat-treated bolts – rolled threaded parts have higher strengths than cut threads in the area where the thread was formed. However, for heat treated parts, rolled or cut threads have the same strength as the heat treatment dictates the strength. Therefore, rolled threads are a way off adding strength to the threads in non-heat treated materials. Specialty Threads The only difference between UNC threads and UNRC threads (or UNF and UNRF threads) is that the root of the thread – the valley that is between the thread “peaks” – is curved/rounded rather than angular. These roots are rounded with an approximate curvature between 0.108 and 0.144 times the pitch. The UNRC and UNRF makes the roundness between threads mandatory, whereas with the UNC and UNF threads the roundness is optional. The reason UNRC threads are produced is because this rounded root helps to improve fatigue strength. UNR stands for unified rounded thread. UNC and UNRC threads are compatible. So, if you are mixing a UNC nut with a UNRC bolt – the threads will still maintain a proper fit. “J” Pitch Threads The biggest trick about J threads is that internal J threads on a nut can be used with standard UNC or UNF threaded bolts, whereas the reverse is not the case. Remember you CANNOT use an external J threaded bolt, screw or stud with a standard threaded nut due to the interference at the minor diameter. | 12 Point Screw Availability |