Exceptional purity and chemical resistance with moderate strength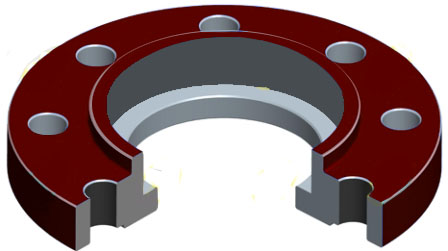
- High Purity and low extractables
- Chemically resistant to most common solvents including acids, salts, oils and steam
- Mechanical strength and toughness to 150°C (300°F)
- Resistance to ultraviolet, nuclear radiation, and standard sterilization methods
- Resistance to weathering and fungi
- PVDF material datasheet
- Socket weld flange features and benefits
PVDF socket weld flanges / Kynar® socket weld flanges are made from a tough engineered fluoro-thermoplastic that offers a unique balance of excellent chemical resistance and good strength properties.
PVDF socket weld flanges have the characteristic stability of fluoropolymers when exposed to harsh chemical and ultraviolet environments but are much stronger mechanically than PTFE or PFA polymers. PVDF socket weld flanges also excel in high purity and low-permeability applications such as pharmaceutical and semi-conductor processing.
Resources: Flange Dimensions, Flange Bolting Chart
Flange Types Available: Blind Flanges, Slip On Flanges, Socket Weld Flanges, Threaded Flanges
PVDF Mechanical & Physical Properties
![]() | ![]() |
PVDF Chemcial Resistance Compared to Other Polymers
Socket Weld Flange Features & Benefits
Similar to a slip on flange, an PVDF socket weld flange has an added shoulder inside the bore hole. The socket weld flange is designed so that a pipe can be inserted into the socket of the flange until it hits the shoulder of the socket. The pipe is then backed away from the shoulder approximately 1/16 inches before being welded to the flange hub. This internal weld provides this type of flange added strength. In addition, by grinding the internal weld smooth, turbulence and flow restriction are minimized. PVDF socket weld flanges are most commonly used on small diameter applications (1/2" through 4") and high pressure piping systems.
Socket Weld Flange Benefits
- Best for small size, high pressure applications
- Static strength equal to a slip on flange yet boasts a fatigue strength 1.5 times that of the slip on design
- Employs both a backside hub weld and an internal shoulder weld for increased strength
- Socket weld flanges delivers a lower risk of leakage than threaded flanges
- Socket weld pipes do not have to be beveled for weld preparation
- Butt-welded joints are easily fitted and no special machining
Socket Weld Flange Disadvantages
- The expansion gap and internal crevices left in socket welded systems can promote crevice corrosion.
- Socket weld flanges have two welds which makes them stronger yet more labor intensive to install. Due to the increased welding, it has become the practice to weld only at the hub of the flange, which is not recommended.
Installation Tips
The socket weld pipe fittings should allow for expansion gap of 1/16 inch (1.6 mm) between pipe and the shoulder of the socket.