Revoseal's lowest leak rate, best sealing semi-metallic gaskets
If your gasket's leak rate is unacceptable as the limits of pressure, temperature & corrosion are being pushed, our line of Revoseal gaskets will be exactly what you are looking for.
Revoseal gaskets are for tough environments and are simply the highest performing, lowest leak rate, semi-metallic gaskets available to industry. If you are having pipe sealing or life issues with spiral wounds, kammprofile, graphite, fiber or PTFE gaskets, our line of Revoseal flange gaskets will be a simple solution to your challenging applications.
Revolution Gasket | Eco+ Gasket | JG/JP Gasket |
![]() | ![]() | ![]() |
Parameters
| Parameters
| Parameters
|
Applications
| Applications
| Applications
|
Advantages
| Advantages
| Advantages
|
![]() | ![]() | ![]() |
JG/JP High Temperature, Pressure & Corrosion Resistant Gasket System
Best sealing gasket for difficult processes & hazardous environments
JG / JP gasket designs create the tightest seal possible for the most extreme high temperature, high pressures and corrosive environments. If leakage in spiral wound, camprofile, or other semi-metallic gaskets are an issue, the JG / JP gasket system may be what you need.
The JG / JP high performance gaskets have a unique design that creates the best sealing gasket available to industry, which is about 15000x better than a spiral wound gasket. Because of its unique metal-to-metal seal, the graphite/PTFE is protected and the graphite will not burn, coke or be attacked by the process. Additionally these gasket can easily be sealed at much lower torques and flange pressure when compared to a spiral wound. The result is far lower leak rates, longer life, high temperatures, and higher pressures can be achieved. This translates into less costs, less product loss, less downtime, less emissions and overall less headaches.
Beyond this unique design, the JG / JP gasket system can also utilize a variety of specialty metals for the most corrosive and high temperature applications. In addition to stainless steel, specialty alloys like duplex, nickel alloys, titanium, Hastelloy, Inconel, Incoloy and tantalum can be incorporated into the gasket.
Finally, the JG /JP designs are completely customizable to fit any flange face or even mismatched flange styles (i.e. grooved to flat face). If you are using spacers, multiple gaskets or other less than ideal solutions, contact Extreme Bolt’s Experts to learn how a custom designed solution can help. These designs can be produced up to 144in / 4000mm in diameter.
Key Benefits
- Lowest leak rate possible, to minimize emissions; Over 15000x tighter seal than spiral wounds
- Designed as a drop-in replacement of spiral wound gaskets
- Customizable designs / Ability to join dissimilar flange faces or large gaps
- Highest temperature alloys & pressure stable design
- Corrosion resistant alloys for dealing with harsh media
- Very low sealing force required: Will not over torque bolts or flanges
- Minimal graphite residue on change out
- Metal-to-Metal seal protects the graphite or PTFE from direct contact with process and degradation
- Available in specialty alloys Hastelloy, Inconel, Incoloy, Duplex, Nickel 200, Titanium and Tantalum
Parameters
- Temperature: Cryogenic to 1830°F / 1000°C (dependent on PTFE or Graphite soft seal option)
- Pressure: From vacuum to 400 bar (1,500 lbs.)
- Specialty alloy options – Stainless, Duplex, Monel, Incoloy, Nickel, Hastelloy, Inconel, Titanium, Tantalum
- Available in any geometry and size – up to 144in / 4000mm diameter
- Thickness: 0.098" to 0.394" (2.5 - 10mm )
- Certs - VDI 2290 per DIN EN 1591, Fire Safe per API 607, and blow-out resistance per VDI 2200
Options
- JG - PTFE substrate with metal backer of choices
- JP - Graphite substrate with metal backer of choice
- Custom Designs - Double seals, leakage detection ports, dissimilar flange surfaces, large gaps
- Vario Self Centering System - Available on both the JG & JP styles allows for easy centering and one gasket to fitt all pressure classes.
Eco+ High Pressure Gasket System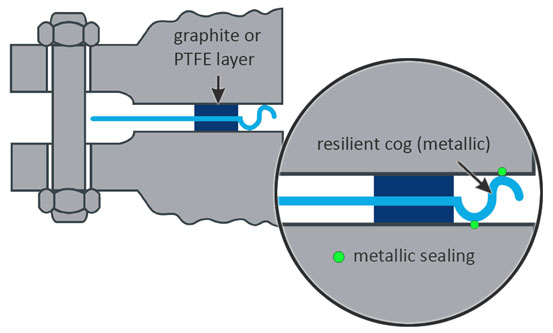
Gaskets for high pressure & harsh steam conditions
The high pressure gasket, Eco+, features a solid flat metallic core encapsulated by PTFE or Graphite and a self-adjusting metal-to-metal spring seal. This spring seal makes the Eco+ gasket ideal for higher pressures as well as cyclic pressure applications. This unique design stabilizes the gasket, as the gasket applies more force to the flanges as pressures increase and surge. This will minimize gasket blow-outs and detrimental gasket deformation. Eco+ is designed to be a higher performing alternative to PTFE and fiber type gaskets and are often used in steam related applications where hammering could be an issue.
Key Benefits
- Very low leak rate: 730x better sealing than graphite gaskets
- Design minimizes the impact of steam hammering & fluctuating pressures
- Self-adjusting spring seal enhances stability & minimizes blowouts
- Very low sealing force required
- High pressure / surge protection
- Minimal graphite residue on change out
- Metal sealing protects PTFE / Graphite
Parameters
- Temperature: Cryogenic to 932°F / 500°C
- Pressure range: from vacuum to 900 psi (160 bar)
- Standard material 316Ti or 316 Stainless (1.4571 - additional materials on request)
- Total thickness 1.6 mm
- Certs - VDI 2290 per DIN EN 1591, Fire Safe per API 607, and blow-out resistance per VDI 2200
Revolution Gasket System
Low leak rate gasket for heat transfer fluids & cyclic applications
The Revolution gasket system features a corrugated stainless-steel backer, which encapsulates either a PTFE or graphite substrate and creates a spring like
interface. The Revolution design is ideal for accommodating flange movement that can be caused by thermal cycling and vibration as the corrugations can expand and contract with the flanges. This allows for a very low leak rate due to consistent sealing pressure that often PTFE or fiber gaskets cannot achieve.
Furthermore, this semi-metallic gasket design isolates the PTFE or graphite substrate from the process with a robust metal to metal seal minimizing leakage and coking.
Available in both 316Ti and 316L, the Revolution gasket system is typically used for heat transfer fluids and oil applications. Often a replacement for fiber gaskets and traditional PTFE gaskets, the Revolution gaskets can be produced up to a 16” in diameter
Key Benefits
- Leak rate 370x lower than graphite gaskets
- Spring like design for consistent sealing
- Very low sealing force required
- Minimal graphite residue on change out
- Metal sealing protects PTFE / Graphite
Parameters
- Temperature: Cryogenic 932°F / 500°C
- Pressure range: From vacuum to 400 lbs (64 bar)
- Standard material 316Ti or 316 Stainless (1.4571 - additional materials on request)
- Available for DIN and ANSI flanges to DN 400 / 16”
- Available with graphite or PTFE substrates
- Total thickness 1.6 mm
- Certs - VDI 2290 per DIN EN 1591, Fire Safe per API 607, and blow-out resistance per VDI 2200
Vario Self-Centering Gasket System
For easy gasket centering & minimizing inventory costs
The Vario centering system available on the JP / JG design, not only ensures perfect centering of the gaskets every time, it consolidates up to 8 flange pressure ratings into ONE gasket.
Key Benefits
- Accurate centering without mistakes, every time
- One Vario gasket fits 8 different flange pressure classes for a given pipe diameter (see example below).
- Huge cost savings and simplification of inventory
Custom Designed Gaskets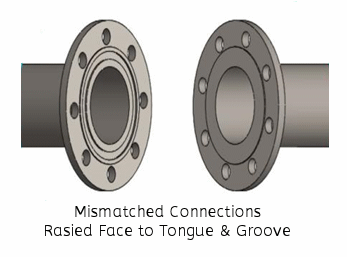
The standard JG / JP are not only the highest performing semi-metalic gasket available, their designs are also completely customizable.
- Connecting dissimilar flanges styles
- Double seals with instrument ports
- Large gaps can be sealed up to 10mm
- Maximum OD of 144in / 4000mm
This is ideal for making leak tight connections with dissimilar flanges styles. For example in the image to the right, you could see a raised face flange can be directly sealed to a tongue & groove flange.
Double seal gaskets can be made and outfitted with an instrument port. In this example, leak detection can be achieved while still containing hazardous media with the secondary seal.
Also because the JG / JP gaskets could be made with a varying thickness between 2.5 - 10mm, large gaps in process connections
could finally be sealed without then need for "homemade" solutions of doubling up gaskets,spacers etc.
Finally with sizes up to 144"or 4000mm, this technology could be applied to virtually any process equipment. If you have a custom design that you would like to discuss, contact our engineers.
Improve Sealing - Low Gasket Sealing Force Required
If you are constantly re-torquing and tightening bolts in an effort to create a seal from a leaky gasket, eventually you reach a limit. This limit comes from either the gasket being over-compressed, the bolts being over-torqued, or the flange being unable to withstand the force and warping. In any of these cases, the connection is compromised.
All the Revoseal gaskets require a very low sealing force when compared to graphite or spiral wound gaskets and will not over-compress like PTFE or graphite.
- No re-torquing required
- Gaskets cannot be over-compressed and deformed
- Easier to seal with weaker bolts and flanges
With all the Revoseal gaskets, they have unique design where a metal-to-metal seal is achieved in addition to the graphite or PTFE seal. This takes relatively little force and creates a robust seal. The image above show how this is achieved. The chart below shows that at the same force applied to the gasket, the JG gasket will have 1000's of times lower leak rate than a competitive gaskets (similarly for the Eco+ and Revolution gaskets). This is a massive improvement.
Metal-to-Metal Gasket Sealing Protects PTFE / Graphite From Process
In all the Revoseal gasket designs, a metal-to-metal seal is created between the gasket and the flange. Because of this metallic sealing, many advantages are created:
- The soft substrate, PTFE or Graphite is isolated from the process
- The graphite / PTFE will not react or contaminate the process
- Graphite will not coke, degrade or burn
- Minimizes graphite residue adhering to surfaces during removal; Little to no cleaning is required
- In the JP design, the graphite is protected from oxygen and can achieve temperatures up to 1832°F / 1000°C
- Protects gaskets from being over compressed
Low Leak Rate Gaskets / Highest Sealing Gasket Possible
If a tight, leak free seal is important to your process, along with reducing emissions and having the safest environment then the Revoseal JP/JG, Eco+ and Revolution gaskets are simple the best option. The Revoseal gasket systems is not just a little bit better than the competition, its orders of magnitude better than the closest competitive options.
Highlights
- JG / JP provides 15,000x better sealing than a typical spiral wound gasket
- Eco+ provides 730x better sealing than tanged graphite gaskets
- Revolution provides 370x better sealing than tanged graphite
Specialty Alloy Gaskets for High Temperature & Corrosive Applications
For high temperature and corrosive applications where stainless materials are not an option, the JG / JP gaskets can be offered with a variety of specialty metal options. Some of the more popular material options for the backer metal are listed below, however of you don't see the material option you are interested, contact our engineers. We most likely can make the JG / JP in the material of your choice.
High Temperature Gasket Materials
- Inconel 600, 601 & 625: The go to material of high temperature applications up to 1830°F / 1000°C
- Incoloy 800 & 825: Good temperature stability up to 1400°F / 760°C
Corrosion Resistant Gasket Materials
- Hastelloy C276 & C22: Great for harsh corrosive media
- Duplex & Super Duplex: Good for moderate acid environments
- Nickel 200: Excellent for caustic and select corrosive conditions
- Titanium: Excellent for sea-water protection
- Tantalum: Only for the most severe acid environments
Minimal Graphite / Fiber Residue On Gasket Change-Out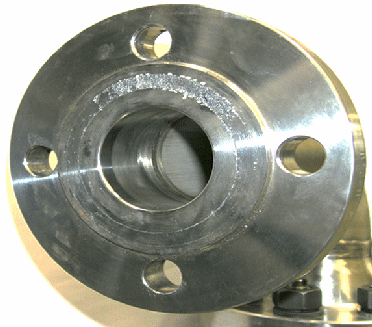
For typical graphite gaskets on change outs, its common for the graphite to be baked on the flange faces, leaving behind a difficult to remove residue. This is due to the graphite being exposed to both the air and process media which leads to a host of problems (below). To avoid these issues, all Revoseal gaskets feature a metal-to-metal seal that protects and isolates the graphite from the process and air. As a result, the following common problems could be avoided (see image to the right).
- Difficult & time consuming cleaning of the flange surfaces
- Remain residue interfering with robust sealing of new gaskets
- Contamination of graphite inside piping
- Increased cost & time of maintenance