An engineered high temperature resistant steel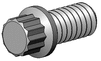
- Excellent high temperature stability and strength
- Very oxidation and carburization resistant to 2100°F
- Good resistance to thermal shock and quenching
- Chemistry and specifications of alloy 330
- Alloy 330 12 point screw features and benefits
- Datasheet for Alloy 330
Alloy 330 12 point screws are specifically designed for high temperature furnace applications such as vacuum furnaces, heat treating and brazing applications. The most prized trait of alloy 330 is its ability perform under cyclic conditions of temperature extremes from heating and cooling; as well as in alternate carburizing and oxidizing atmospheres. An austenitic, nickel-chromium-iron-silicon alloy, 330 12 point screws also offer industry a low coefficient of expansion, excellent ductility, and high strength.
Benefits & Corrosion Resistance
- Resistance to thermal shock from repeated quenching
- High level of resistance to oxidation and carburization
- Ability to handle thermal cycling
- Provides resistance to scale formation up to about 2000°F
- Good resistance to nitrogen-containing atmospheres where the oxygen content is low
- High nickel content of 34-37% provides high resistance to chloride stress corrosion cracking and embrittlement
Applications for Alloy 330 12 Point Screws
- Alloy 330 screws are often used in furnaces, thermal processing and heat treating applications.
- Gas turbine components and boiler fixtures used in power generation often use Alloy 330 12 point screws.
- Because of its resistance to nitrogen rich environments, alloy 330 screws are used extensively for components handling cracked ammonia.
Alloy 330 Properties | |
Tensile Strength (ksi) | 80-85 |
Yield Strength (ksi) | 30-43 |
Elongation in 2” | 40-45 |
Rockwell B Hardness | 70-85 |
Density (lb/in3) | 0.292 |
Specific Heat (Btu/lb/°F (32°-212°F) | 0.11 |
Modulus of Elasticity Tension | 28.5 |
Resources: Alloy 330 Torque Specs
Alloy 330 Screw Types: 12 Point Screws, Button Head Cap Screws, Flat Head Screws, Hex Head Cap Screws, Pan Head Screws, Set Screws, Socket Head Cap Screws, Tamper Resistant Security Screws, Torx Screws, Vented Screws
Alloy 330 12-Point Screw Features & Benefits
The driver of a alloy 330 12-point screw uses two overlapped hexagon shapes, creating 12-points and a flanged underside. These are also referred to as ferry cap screws or 12 point flange screws. The advantages of this head style include:
- Higher torque capability compared to a socket head cap screw
- Lack of recess to trap fluid or debris.
- As the heads are generally smaller than a hex, alloy 330 12-point screws are often used situations where installation space is tight and saving weight is critical.
The overall disadvantage is the extra cost involved in forming the heads.
The Controversy of 6 vs. 12 point Bolts
There is much debate over which bolt is better. Some say that the more points a nut or bolt has – such as a 12-point bolt - the less chance you have to round it off. And that the additional contact points of a 12 point screw give you more surface to apply load. While the jury is out as to the accuracy of this, it’s the application that should dictate whether the benefits of a 12 point screw out weight the additional costs of making them.
Alloy 330 Chemistry and Specifications
Alloy 330 (UNS N08330) is best known for its extreme high temperature strength and stability. One of the most unique attributes of Alloy 330 is its ability to handle cyclic temperature changes from extreme high temperatures to cooling phases, as well as in oxidation-rich environements.
Alloy 330 Specifications: UNS N08330, AMS 5592, AMS 5716, ASME SB 511, ASME SB 536, ASTM B 511, ASTM B 512, ASTM B 535, ASTM B 536, ASTM B 546, ASTM B 710, ASTM B 739, EN 10095, Werkstoff 1.4886