A Ni-Cr alloy with very good high temperature stability
Good high temperature strength
- Oxidization and carburization resistant at high temperatures
- Good corrosion resistance, which increases with the various grades
- Weld neck flange features and benefits
- Download the Incoloy 800 datasheet and 825 datasheet
Not to be confused with Inconel, Incoloy weld neck flanges are made of a nickel alloy which contains iron and a lower content of nickel. Incoloy is essentially a more economical option to Inconel, yet with more restricted corrosion resistance and temperature limits. Typically, Incoloy is an ideal material for long-term exposure in high temperature environments due to its oxidation, carburization and creep resistance. Incoloy is widely used for its resistance to seawater, brine, sour gas and high chloride environments at elevated temperatures, which make it a popular choice in the oil and gas and power industries.
The most commonly used grades of Incoloy flanges are Incoloy 800, 800H, 800HT;Incoloy 825; and Incoloy 925. For more indepth information on these specific grades, visit our specific web pages or contact one of our engineering experts:
Resources: Incoloy Torque Specs, Flange Dimensions, Flange Bolting Chart
Incoloy Fastener Types: Bolts, Nuts, Screws, Threaded Rods, Washers
Flange Types Available: Blind Flanges, Lap Joint Flanges, Slip On Flanges, Socket Weld Flanges, Threaded Flanges
Common Incoloy Chemistry, Grades & Specifications
Incoloy 800, 800H, H00HT
Incoloy 800 series flanges are best utilized for applications that require stable structure and good strength during prolonged exposure to high temperatures.
Incoloy 800, 800H & 800HT Specifications: UNS N08800/ N08810 / N08811 (800, 800H, 800HT), ASTM B408, ASME SB408, ASTM B564/ASME SB564, EN 10204-3.1, Werkstoff 1.4876 (800), Werkstoff 1.4876 H and 1.4958 (800H), Werkstoff 1.4876 HT and 1.4959 (800HT)
Incoloy 825
Related to the Incoloy 800 series alloys, Incoloy 825 differentiates itself with the additional elements of molybdenum and copper, which provides it improved corrosion resistance.
Incoloy 825 Specifications: UNS N08825, , BS 3076NA16, ASTM B 425, ASTM B 564, ASME SB 425, ASME SB 564, ASME Code Case N-572, DIN 17752, DIN 17753, DIN 17754, VdTÜV 432, ISO 9723, ISO 9724, ISO 9725, Werkstoff Nr 2.4858
Incoloy 925
Incoloy 925 is a precipitation hardened alloy. It offers comparable corrosion resistance to it’s sister alloy Incoloy 825, but with the increased strength resulting from the age hardening process.
Incoloy 925 Specifications: UNS N09925, ASTM B637, NACE MR0175
Mechanical Properties of Incoloy
Incoloy Weld Neck Flange Features & Benefits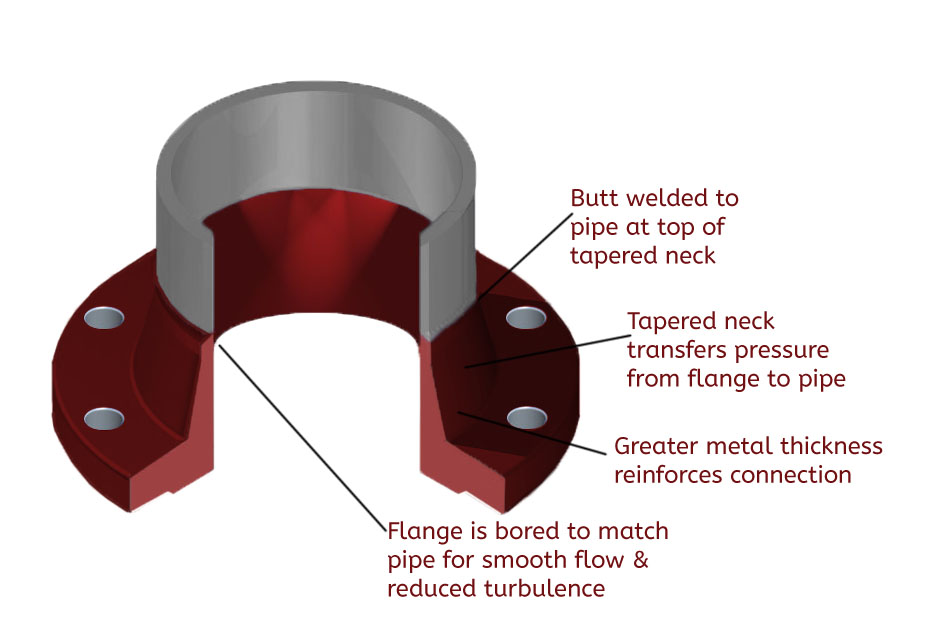
Incoloy weld neck flanges are best for hazardous, high pressure applications. Weld neck flanges are easily identified by their long tapered neck. The inside of the flange is bored to match the inside diameter of the pipe in order to ensure there is no restriction in flow and also to prevent turbulence at the joint. The tapered neck provides thicker metal at the flange joint, while the neck narrows down gradually to meet the pipe where it is butt welded to the pipe. This design helps to transfer stress from the flange to the pipe, as well as diminish stress concentration at the base of the flange connection.
Incoloy weld neck flanges are ideal for critical applications involving high pressure, sub-zero and elevated temperatures, as well as in conditions where fluctuations cause pipe expansion/contraction.
Key Feature: Ideal for high presure applications.
Weld Neck Flange Advantages
- Ability to withstand high pressure – since pipe is welded to the neck of the flange, stress is transferred to the pipe.
- The beveled end that, when connected to a pipe, creates a trough for a strong weld.
- Most versatile flange in the ASME stable of flanges.
Weld Neck Flange Disadvantages
- More advanced welding skill is needed for installation. The inside weld must be smooth to reduce friction and the outside weld must meet code criteria.
Uses
- Severe conditions that include high-pressure, high-cyclic and hazardous fluid applications.
- Fitting-to-fitting fabrication where the flange is welded directly to a fitting, such as an elbow, without the need for a short piece of pipe, as would be required with a slip-on flange.