For strong acids and severe corrosion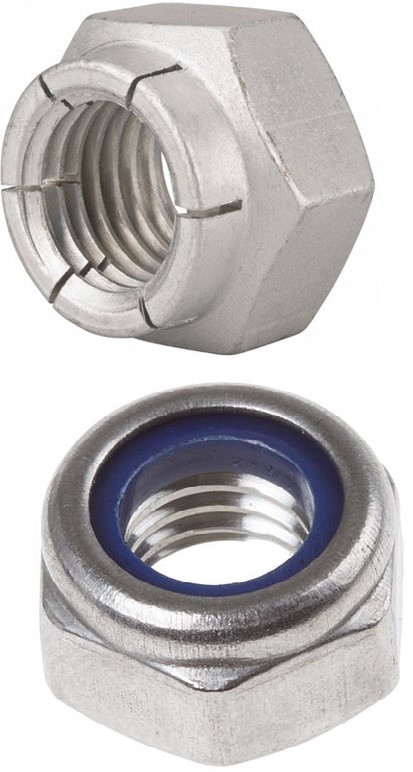
- Good mechanical & physical properties
- Excellent corrosion resistance (HCl and H2SO4 iso-corrosion curves)
- Zirconium 702 / 705: Grades, chemistry, specs
- Datasheet for Zirconium
- Zirconium lock nut features and benefits
Commercially pure zirconium lock nuts, also known as zirconium 702, are most well-known for their superior corrosion resistance in some of the harshest environments that include:
• Hydrochloric Acid | • Sulfuric Acid | • Formic Acid | • Nitric Acid | • Acetic Acid |
It is also a metal that offers industry unique properties. It does not absorb neutrons, making it ideal for use in nuclear power and at low temperatures it is superconductive, making it ideal for super magnets.
Hydrochloric Acid Resistance
What makes Zirconium lock nuts particularly useful to industry is their resistance to hydrochloric acid where they exhibit a corrosion rate of less than 5mpy at all concentrations and temperatures in excess of the boiling point. Even in 37% HCI, Zirconium lock nuts do not begin to show substantial corrosion until 130°C (266°F). This performance is unmatched by any other engineering metal or alloy with the exception of tantalum. To give you a point of reference, Hastelloy C276 will experience 288 mpy (mils per year) of corrosion in just 10% HCl at the boiling point while Zirconium lock nuts will have a nil corrosion rate even when aerated. As a result, Zirconium lock nuts are most beneficial when used is in hydrochloric acid processes with temperatures above the boiling point and in the absence of oxidizing impurities.
General Acid Resistance
In addition to its impressive performance in hydrochloric acid, in sulfuric acid, Zirconium lock nuts are resistant to temperatures well above boiling and at acid concentrations up to 70%. Only one other metal, tantalum, is equal to zirconium in nitric acid, where zirconium can be used in all concentrations up to 90% and temperatures up to 200°C. Zirconium is also resistant to most organic media and is considered one of the most corrosion resistant materiala in virtually all acetic acid solutions.
When Zirconium Does Not Perform
Zirconium is known for its tough resistance to acid corrosion, but there are instances that it is not recommended to use Zirconium. Though aeration does not affect the resistance of Zirconium lock nuts, even small amounts of oxidizing media such as ferric or cupric chlorides will greatly decrease its corrosion resistance. This often occurs from upstream equipment that carry corrosion contaminants into the zirconium equipment, making process control of upstream equipment critical in maintaining the corrosion resistance of Zirconium. In addition, acid in the presence of oxidizing halide contaminants and can accelerate the rate of attack on Zirconium lock nuts even at low concentrations. Use of Zirconium lock nuts in the presence of fluoride ions is also not recommended, even at low concentrations.
Applications
• Nuclear industry utilize Zirconium lock nuts for its inability to absorb neutrons
• Zirconium has been used for decades in over 20 years in dye manufacturing for its incredible corrosion resistance and inertness.
• Chemical processing plants often utilized Zirconium in the production of polymers that utilize strong acids .
• Commonly used with nitric acid for the production ammonium nitrate for fertilizers.
Resources: Zirconium Torque Specs
Zirconium Locknut Features and Beneifts
A zirconium locknut resists loosening from vibrations and torque. One of the most common styles is a prevailing torque locknut. This kind of zirconium locknut has a prevailing torque feature which deforms elastically, preventing it from freely spinning like a standard nut.
The two most common and reliable forms of prevailing torque locknuts are the flexloc style and the polymer insert lock nut. A zirconium flexloc nut is all-metal in composition with a segmented collar that creates six “locking fingers,” that act as a spring. Zirconium polymer insert lock nuts are often referred to as nylon insert locknuts, although various high performance polymers can be used for the screw threads to “bite into.” Both flexlock and polymer insert locknuts are available in both hexagonal and 12 point configurations.
All Metal Flexloc Lock Nut![]() | ![]() |
|
|
Other all metal lock nuts available include the zirconium stover and elliptical styles. Though these styles are often a cheaper initial cost, they are less reliable than the flexloc style. As these styles delivering less prevailing torque cycles and often result in more failures, the flexloc style is a better investment for both reliability and cost savings.
Zirconium Grades, Chemistry and Specifications
Zirconium 702
99.2% commercially pure zirconium with the highest corrosion resistance.
Zirconium 702 Specifcations: UNS R60702, ASTM B493 and B550, ASME SB493 and SB550 Rod (Bar), ASTM SB551, ASME SB551 Plate, Sheet and Strip
Zirconium 705
95.5% zirconium with the addition of 2-3% niobium. This addition increases the impact strength of the alloy.
Zirconium 705 Specifications: UNS R06705, ASTM B493 and B550, ASME SB493 and SB550 Rod (Bar)
Mechanical Properties
![]() | ![]() |
Zirconium Iso-Corrosion Curves